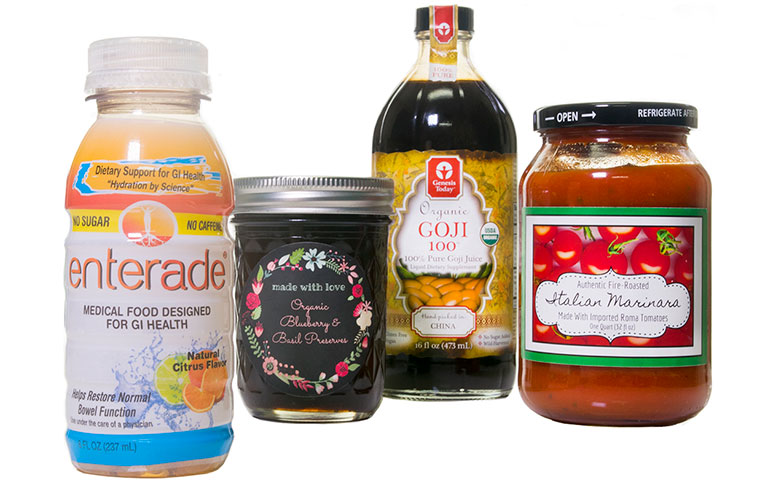
“Hot filled” refers to the pasteurization process for certain types of beverage and food products to ensure safe consumption and a longer shelf life without the use of preservatives. Hot filling contents into a bottle requires equipment that can heat, cool, and cap the product. In this article, we’ll explain how hot filling works, which containers to use for hot filling, and what to consider when labeling hot filled bottles for a seamless packaging process.
Overview of Hot Filling Process
Hot filling is a popular method for filling acidic beverages and foods (pH of less than 4.6) that need to be shelf stable at ambient temperatures. Unopened hot filled products can last up to 12 months.
How hot filling typically works:
- The beverage or food liquid is heated to 194 degrees Fahrenheit.
- The heated liquid is injected into a container and capped.
- The container is tilted to a precise angle which allows the heat to sterilize the container and the cap.
- The container passes through a cooling tunnel that uses a water spray system to reduce the temperature, thereby preserving the product’s integrity and taste.
- An air dryer removes remaining water from the container in preparation for labeling and secondary packaging.
Although hot filling is a safe and relatively easy way to pasteurize beverage and food products, not all products are compatible with the hot fill process.
Products That Can Be Hot Filled
Low acid beverages and foods, or those with fiber or pulp, aren’t compatible with hot filling because spores are more likely to survive after sterilization. Furthermore, some contents can even be subject to degradation or spoilage when exposed to high temperatures. The beverage or food must have a pH level less than 4.6 (acidic) to ensure that bacteria will not grow in the remaining spores. Substances with a pH of 4.6 or higher (alkaline) are subject to multiple spores and therefore aren’t considered safe for hot filling.
Types of products that can be hot filled:
- Fruit and vegetable juices
- Teas
- Sports drinks
- Enhanced waters
- Sauces
- Marinades
- Spreads
- Soups
Hot filling a product removes the need for preservatives without damaging the product’s taste, vitamins, and nutrients which is why the right temperature is crucial for success.
Temperature Monitoring Is A Must
Before we discuss containers, it’s important to note that hot filling requires constant monitoring. Temperature plays a key role in the hot fill process and if it becomes too low, microbiological agents may develop which pose a health and safety risk. That’s why hot fill manufacturing often includes a recirculation system that keeps production moving with a backup system in place if a container or the liquid drops below a pre-set temperature.
Selecting The Right Container
There are several different containers that can be hot filled such as glass, heat resistant cans, and certain plastics. Hot temperatures make standard PET bottles change shape or collapse so manufacturers who want to use plastic bottles will need to use ‘heat set’ PET bottles that are designed to handle hot filling. These specialty bottles are heavier in the body, neck, and cap in order to withstand the heat. It’s important to note that since heat set bottles are heavier and more complicated to produce compared to standard PET, they tend to cost more.
There are a variety of hot fill equipment lines that accommodate different container types and sizes. Whether you decide to buy your own hot fill equipment or work with a co-packer, make sure your container is compatible with all the filling, labeling, and packaging equipment.
Labeling And Secondary Packaging For Hot Filled Products
After cooling and drying, the product is ready for labeling. You or the co-packer will need application equipment that will work with your pressure sensitive roll labels or shrink sleeves. If you have pressure sensitive labels, then a rotary labeling machine (also called ‘rotary labeling system’) or an inline automatic labeling system will be needed depending on the production line and output. Other considerations that will need to be taken into account are label adhesives, size, material, and placement (i.e. front and back, top and bottom, neck and shoulder, or wrapped around.) Adhesives are particularly important because a special adhesive will need to be used for hot filled containers.
Unlike pressure sensitive labels that use adhesives and are applied by pressure, shrink sleeves are shrunk onto the container using mechanical shrinking equipment like a steam tunnel, radiant heat tunnel, hot air tunnel, or hybrid tunnel (combines heat and steam). We recommend using a steam tunnel for shrink sleeves because it uses less energy to run than other types of tunnels, produces better results, and is easier to configure.
Steam tunnels are becoming the label industry’s standard method of shrinking sleeves onto filled product containers because its relatively low temperatures (usually between 170-180 degrees) make it safe for filled products to pass through.
Final Step: Secondary Packaging
Once the product has been labeled, it heads off to the secondary packaging station where a certain quantity of products are packed together for shipment. Secondary packaging allows for easier product protection, handling, palletization, and transportation. Popular options include:
- Cardboard boxes
- Shrink wrapping
- Carton trays
- Plastic crates
Depending on your product and transportation needs, you will likely find that a certain secondary packaging is more suited for you than another. Discuss with your co-packer or packaging equipment vendor to see which secondary packaging is right for you.
Getting Custom Labels For Hot Fill Products
When ordering custom labels, make sure to mention that your product will be hot filled. Containers and labels expand and contract when heated and cooled which can cause the label to wrinkle and bubble (this issue is more pronounced with plastic containers than glass). Letting us know that you will be labeling a hot filled product and the container type will ensure that a special adhesive will be used to avoid label issues. We recommend testing label materials before investing time and resources into an order.
As you can see, there are a variety of factors that need to be considered to create a streamlined filling and packaging process. Whether you acquire your own equipment or use a co-packer, it’s essential that you research different types of hot fill, labeling, and secondary packaging equipment to ensure that they are compatible with your container and labels, as well as with each other.
Once you have the right equipment and label artwork, contact our customer service team to get custom printed labels or shrink sleeves for your hot filled product.